EU declaration conformity
Frequency inverter 230 V | control switches | 4.3 A | 0.37kW | IP66
Product description
Simple variable frequency drive (VFD) for controlling single-phase motors. It is intended to control the speed of fans or pumps in HVAC systems.
This frequency drive can regulate single-phase permanent split capacitor or shaded pole induction motors.
It has a built-in potentiometer, run-stop switch and mains disconnector. Simply wire up the drive, turn the inbuilt potentiometer and the motor will start running.
This variable frequency drive can control motors with a maximum (combined) current of 4.3 A. The supply voltage is 230 V AC. The integrated EMC filter is Class C1.
The enclosure is dust-tight and washdown ready. It offers an IP66 protection against ingress of dirt and water. The heatsink is corrosion resistant.
Manufacturers code: ODE-3-120043-1F1B-01
Documents
Additional specifications and description
How does this frequency inverter provide reliable control for single-phase motors?
What makes this inverter so durable?
The enclosure is designed to protect the electronics even in harsh environments or in outdoor applications. It offers an IP66 protection against the ingress of water, dirt and contaminants. This makes it possible to install this frequency inverter directly on the installation, even in high-pressure wash-down applications. It eliminates the need of an electric cabinet. It is advisable to protect the device against snow and direct sunlight.
What are the integrated motor controls?
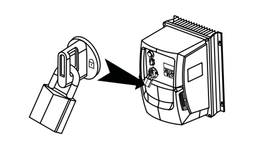
This frequency inverters features a potentiometer to regulate motor speed. Motor speed can be adjusted infinitely variable. Below the potentiometer, there is a 3-position switch to start and stop the motor. In case of a single-phase motor, the motor will always run in the same direction. Via the switch disconnector, the mains (supply voltage) can be disconnected. This switch disconnector has a padlockable OFF position to guarantee that the frequency inverter remains disconnected from the supply voltage during maintenance for example.
What is the technology behind the optimal motor control?
Frequency inverters control motor voltage and motor frequency via a technology called pulse-width modulation. This technology converts the supplied AC voltage into DC voltage. A frequency inverter has a DC bus, which can be seen as a buffer tank for the available energy. This buffer tank is filled both by the supply voltage (via the rectifier) and by regenerative energy from the motor that flows back during braking. This DC voltage is converted back into a kind of alternating voltage by IGBTs. IGBTs or Insulated Gate Bipolar Transistors are bipolar transistors with an insulated gate terminal that can switch high electrical current at high speed. Thanks to the smart control of the IGBTs, both the motor voltage and the motor frequency can be controlled. This enables optimum motor control and energy-efficient operation.
What are the additional features?
A disadvantage of high-frequency switching IGBTs is the fact that they pollute the electrical network with higher harmonic interference signals (EMC pollution). To minimize this network pollution, an EMC filter class C1 is built in as standard. This frequency inverter is also equipped with an integrated brake chopper. This makes it possible to connect a brake resistor to reduce the deceleration time if necessary. Sentera HVAC sensors can be connected via the analogue input or via Modbus RTU communication.
Remarks, reviews & ratings